The primary processes carried out by Cold Formed Products are impact extrusion and forging or a combination of the two.
The processes are well known for the production of containers such as toothpaste tubes and aerosol cans, but their full potential for the production of high integrity components is not widely known. We have specialized in this area and have developed tooling techniques we believe to be unique.
The COLD FORMING or FORGING process in particular consists of placing an aluminium ‘slug’, often like a thick coin, into the die of a press and striking it with a punch. The resultant impact pressure causes the slug to fill the die and form into the shape of the cavity between the die and punch at high speed and pressure.
FORWARD EXTRUSION will take place if material is allowed to flow forwards through an orifice in the die.

BACKWARD EXTRUSION will take place if material is allowed to flow backwards up the punch surface.
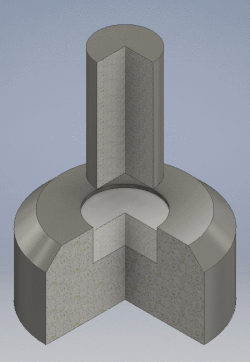
FORWARD & BACKWARD EXTRUSION

By combining BACKWARD & FORWARD EXTRUSION and even FORGING is possible to produce highly complex parts in one pressing operation. This, coupled with high material utilisation, yields a component which, in addition to being structurally superior, is very cost effective.
A virtually infinite variety of shapes and sections can be introduced into the part by varying the design of the tool set. For more conventional components impact extrusion can frequently replace die casting or turning with substantial advantages.
We also carry out a huge range of secondary machining operations, including high precision CNC machining, on parts that we produce by extrusion and/or forging or on special bought-in sections.